La Válvula de Espiración controla la presión de salida del flujo de aire del paciente ( Figura 1 ) . Trabaja a muy poca presión y es necesario que tenga poca carga. Se decidió imprimir esta pieza en 3D para tener la flexibilidad de diseño y disponibilidad para el proceso de producción ( Figura 2). La actuación sobre la válvula será por medio de un motor stepper de 200 pasos por revolución.
Es importante recordar que un paciente COVID-19 puede estar 14 días conectado a ventilación mecánica, por lo que las partes deben soportar al menos 1,2 millones de ciclos de funcionamiento.
Modelo Inicial
El diseño incial permitía controlar el flujo y la presión de la espiración de manera proporcional, algo muy deseable para los sistemas de control automático.
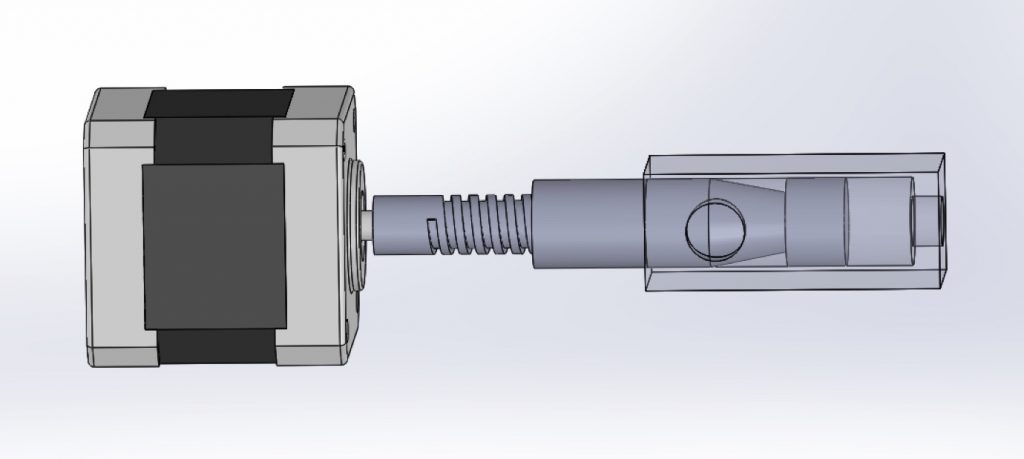

Se realizaron algunas pruebas con este diseño, sin embargo, no fue posible determinar con certeza la vida útil de la válvula producto del desgaste entre sus piezas.
Segunda Iteración
Dado lo anterior, se buscó una solución que diera la proporcionalidad en el control, pero que también permitiera asegurar un desgaste mínimo y la menor pérdida de flujo posible. Por esta razón, se cambió el diseño por el detallado en la Figura 3 , en donde el aire entra por la punta del cono y sale por un ducto lateral en la parte superior. El eje del motor stepper desplaza la válvula por medio de un hilo.
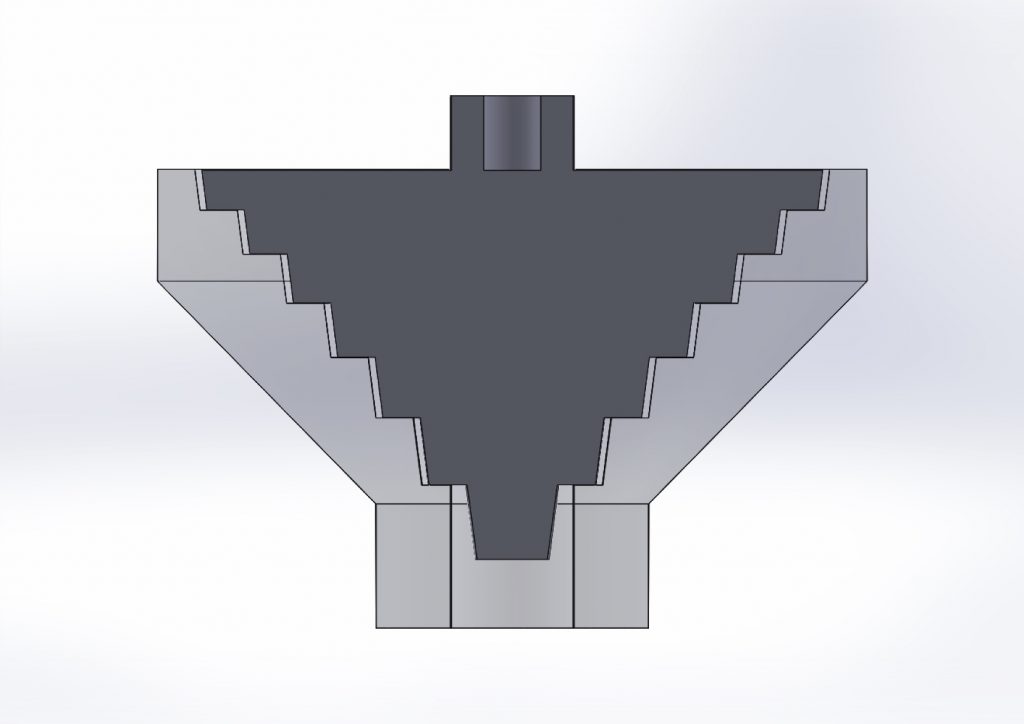
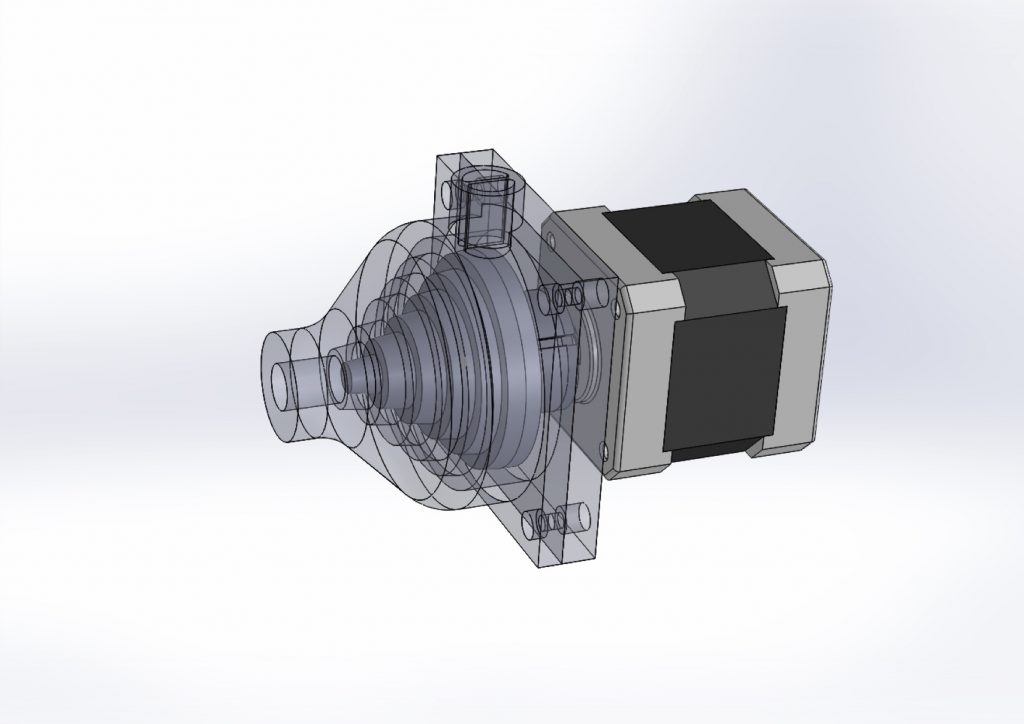

Proceso de impresión 3D
Es importante mencionar que el proceso de impresión toma 8 horas y se imprimen todas las piezas juntas.


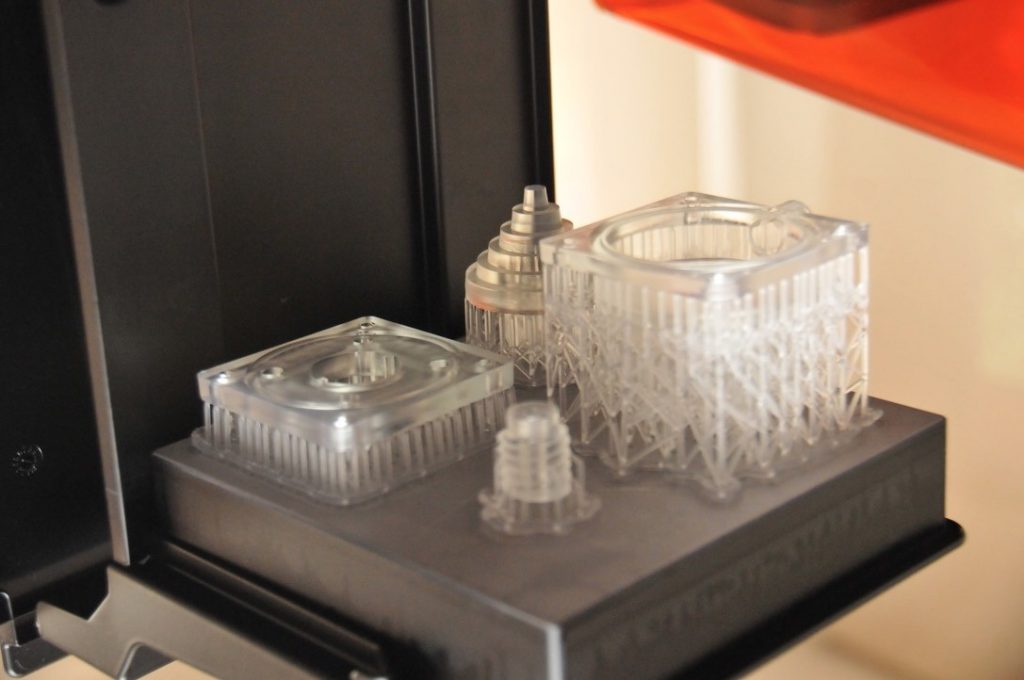
El proceso de curado con luz UV de la resina impresa, toma cerca de 1 hora y permite darle a cada pieza, la dureza necesaria para soportar la carga de trabajo.
La válvula ensamblada queda de la siguiente forma, detallada en la Figura 10.


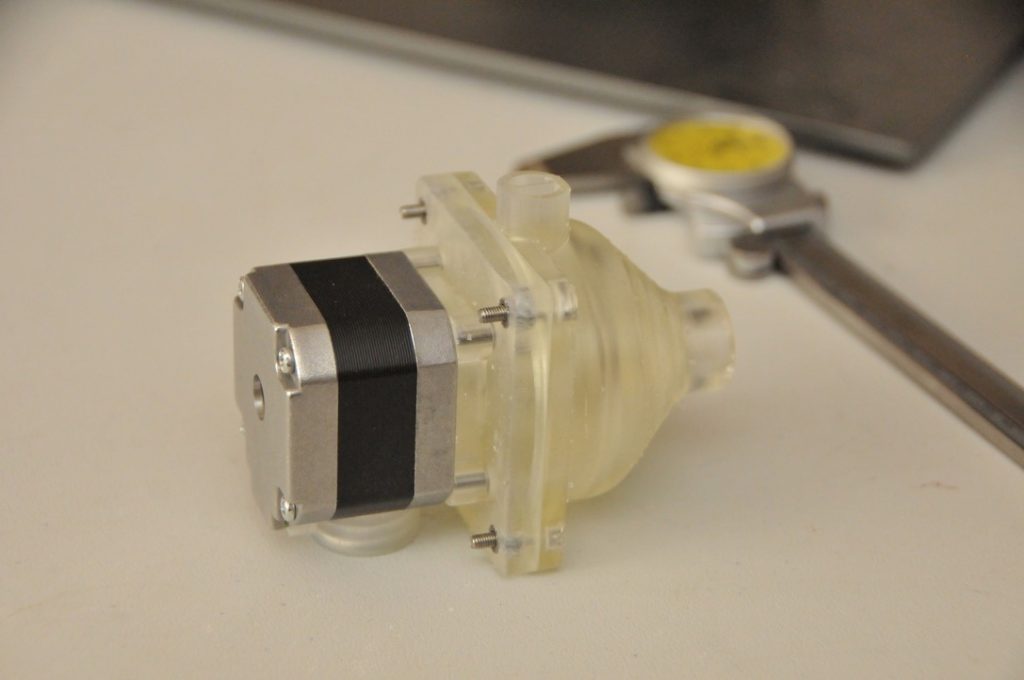
El próximo paso es realizar pruebas de estrés a la válvula y determinar si será capaz de resistir los 1.2 millones de ciclos que requiere el diseño.